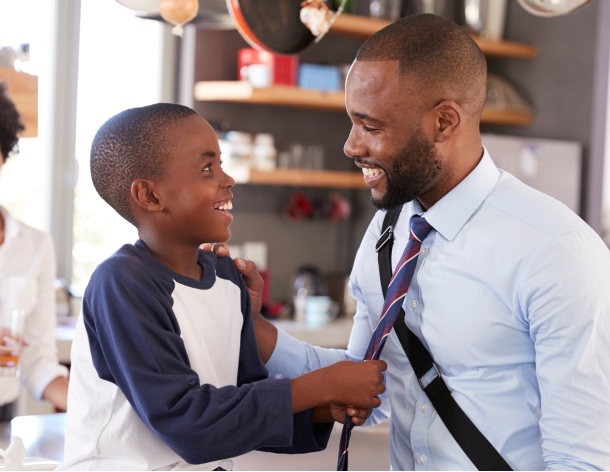
Long-time president, chairman, and CEO of General Motors Alfred P. Sloan Jr. once said: “Only in more production and in new production can the American standard of living be increased and the economy be sound.” Manufacturers contribute $2.81 trillion to the U.S. economy annually; for every $1.00 spent in manufacturing, there’s a total impact of $2.60 on the economy.
Every year, manufacturers nationwide create billions of dollars in product output, manufacturing talent shortage worsens. It’s a hiring drought that has persisted for decades. The Department of Labor’s database shows the losses in skilled employees in this sector from 2002 to 2021.
There were 803,000 manufacturing job openings in January 2023. Given that around 2.6 million retirements are expected in the industry over the next decade, the industry is estimated to have 2.1 million unfilled jobs by 2030. Some 224,000 manufacturing jobs were brought back to the U.S. from overseas in 2021, but U.S. manufacturers don’t have the skilled workers they need to take on these reshored production contracts.
The U.S. government announced in May 2022 that there were 4,300 projects underway, to which $110 billion in federal funding had been allocated. According to the Biden administration, the infrastructure program will create 556,000 new jobs, many of which are in manufacturing. The question is, who is going to fill these roles? The opportunity for manufacturers to grow their operations is there, but without qualified workers, they have to leave money on the table.
Let’s explore ways your business can evolve to address the manufacturing talent shortage by attracting a younger and evolving workforce. To identify these solutions, it’s crucial to understand the blockers that stop today’s eligible talent pool from pursuing careers in manufacturing.
The manufacturing talent shortage is a complex and multifaceted issue. Here are some contributing factors:
Southern and western U.S. states saw the highest recent growth in manufacturing for employment and GDP. Nevada saw nearly 50% growth in manufacturing employment and GDP from 2010 to 2020, while California had a 45.6% increase in GDP.
However, the cost of living in these states is also high. The cost of living in Nevada is 1.05 times more expensive than the average in the United States. California’s housing cost-of-living index is on par with New York’s, coming in 94% higher than the national average. While the Southern U.S. is known to be less expensive than the east and west coasts, home prices have increased by more than 60% in just five years in North Carolina, South Carolina, Tennessee, and Florida.
70 million U.S. workers can do their jobs remotely, a third of the total workforce. Many workers, particularly younger generations, have come to value the flexibility and convenience of remote work.
Manufacturing jobs often require workers to be physically present in the factory or plant to operate machinery, handle equipment, or perform assembly line tasks, making it difficult to attract workers who want more flexibility.
The average manufacturing entry-level salary is $31,366 annually or $15.08 per hour. Given these relatively low wages, manufacturers compete with Walmart, Target, Amazon, and UPS, which offer higher entry-level wages and bonuses.
In addition, the rise of the gig economy has also posed a challenge for manufacturing employers. Gig workers used to same-day pay may not apply to jobs that will pay them every few weeks.
To address the manufacturing talent shortage, manufacturers are investing in employee training and partnering with local education institutions to offer credentialing paths. However, these efforts alone may not close the gap at the rate the economy needs.
To attract and retain skilled workers, manufacturing employers need to think creatively and offer new benefits. On-demand pay is a solution gaining traction across many industries with staffing shortages. These benefits help employees living paycheck-to-paycheck avoid payday loans and increase their financial security. Financial wellness benefits can also help your manufacturing business compete with industries that pay their employees same-day.
By adapting their compensation packages to include on-demand pay, manufacturing employers can attract a younger, more diverse workforce that values flexibility and convenience. By investing in their employees’ financial wellness and adapting to changing preferences, manufacturers can help bridge the talent gap and secure a stronger future for their businesses and the broader economy.
Key takeaways: Automated cashless tips provide a secure and efficient way to...
The heart of every business is its employees, and these employees need to be...
February is Black History Month, a time to honor the rich history, vibrant...
© 2025 Payactiv, Inc. All Rights Reserved
24 hour support: 1 (877) 937-6966 | [email protected]
* The Payactiv Visa Prepaid Card and the Payactiv Visa Payroll Card are issued by Central Bank of Kansas City, Member FDIC, pursuant to a license from Visa U.S.A. Inc. Certain fees, terms, and conditions are associated with the approval, maintenance, and use of the Card. You should consult your Cardholder Agreement and the Fee Schedule at payactiv.com/card411. If you have questions regarding the Card or such fees, terms, and conditions, you can contact us toll-free at 1-877-747-5862, 24 hours a day, 7 days a week.
** Central Bank of Kansas City does not administer, nor is liable for earned wage access.
Payactiv holds earned wage access services (EWA) license number 2591928EWA with the Wisconsin Department of Financial Institutions.
Apple and the Apple logo are trademarks of Apple Inc., registered in the U.S. and other countries. App Store is a service mark of Apple Inc., registered in the U.S. and other countries.
Google Play and the Google Play logo are trademarks of Google LLC.
Galaxy Store and the Galaxy Store logo are registered trademarks of Samsung Electronics Co., Ltd.